装备制造业数字化的内涵策划与实施
Posted 数商云网络
tags:
篇首语:本文由小常识网(cha138.com)小编为大家整理,主要介绍了装备制造业数字化的内涵策划与实施相关的知识,希望对你有一定的参考价值。
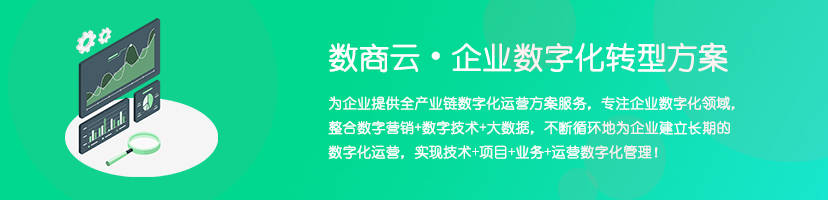
一、前言
信息化技术已成为现代产业变革升级的发动机。“中国制造2025”明确,新一代信息技术与制造业的深度融合,已成为现阶段中国实施制造强国战略的主线工作。大型装备制造业亦如此,要在信息化时代浪潮中保有话语权,必须逐步实现数字化、网络化、智能化[1],助力企业转型升级,打造良好创新基础,提质增效,化解系统性质量风险,保证自身竞争力。
二、数字化对装备质量管理的重要意义
我国装备制造业信息化水平普遍不高,缺乏数据采集、分析的有效途径,大部分还是以纸质资料作为载体,纸质的数据信息存在以下方面的缺点:
1.纸质工艺卡流转慢,漏项风险较大,易丢失,且过程数据记录个性化,记录不规范、全面。一件产品,可能有多个零部件,工艺卡拆分流转困难,常造成流转卡与实物脱节,无法有效保证“三按”生产。出具报告时,个性化明显,记录版本多样,数据未标准化、结构化,后期要提取、分析较困难。
2.数据的集成性低,信息传递效率低,检索时间和人员成本高昂,无法快速追溯。装备制造过程中会形成很多纸质数据记录、报告,质量管理人员需耗费大量精力去收集整理,确认资料的合格性、完整性,工作效率低。而随着产品的发运,资料被归档到档案馆某个角落,前期收集、记录的大量数据便失去了它的价值,当产品在使用过程中出现问题,需要调查原因时,资料难以查询。
3.质量资料归档、保存压力大,质量证明书编制耗时耗力,重复性劳动多。大型装备制造业,均需要专门的档案楼宇归档产品资料,保存期有限,在倒运过程中遗失、损毁风险大,没有备份,难以复原。质检人员收集过程资料后,一般还需在原始资料中逐一提取信息,编制质量证明书,汇总成册发送用户审阅留档,过程耗时耗力,且誊写错误率高,影响企业形象。
当今企业设备越来越智能化,若生产不实现数字化,已很难适应现代化企业的发展需求,智能设备功效也难以完全发挥。不建立起产品质量数据库,保证质量数据追溯,全生命周期质量管理只能是空谈。我们的企业改进、创新同样需要数据的支撑,卓越绩效模式、六西格玛管理、精益生产等方法运用,必须要有丰富的数据作为依托,才能有效分析、改进,促使生产过程的无缝衔接和企业间的协同制造,实现生产系统的智能分析和决策优化。因此,数字化是企业通往现代化的前提,必须提早规划部署。
三、装备制造业数字化的方向
大型装备制造不同于简单流水作业,其涉及材质、部件多样,制造工序复杂,过程问题多变,生产数据繁杂,且自动化水平普遍不高。要实现数字化、信息化必须全盘规划,精准落实,确保我们以最便捷、直观的方式获取产品的重要数据并分析使用。
1.技术文件资料的结构化
现代企业一般都有PLM、BOM等主流技术系统,但部分技术内容却未标准化、结构化,系统间难以有效识别和自动调取。因此,我们首先要做的就是对源头数据的结构化,给予它可识别的身份标识,这是实现数字化的基础工作,保证系统间可以实现相互串联和共享。制造工艺流程和产品设计信息,一般都是企业的生产主线,是数字化系统的主干,我们的生产过程执行都是以此为依据和指导,特别是生产工艺,作为我们生产的主线,应作为主干,生产过程数据要以此为依托,挂在各个生产节点上,实现全过程的质量管控。所以,主干上能自动调用的基础数据越多越好,可以减少大量基础输入工作,提升使用体验,切实保证数字化的推行。
2.控制节点的梳理和确认
根据产品的生产特点、难点及标准、体系要求,合理设置工艺流程控制点,既要保证对过程质量的有效监督,又不宜事事监管,确定关键节点做好把控,同时,保证生产的流畅。各个控制点,应设置数据录入接口,检查人员检验后应及时地录入检验结果,生成报表,保证数据收集的便捷、及时、有效。前期需要统筹规划,对各项检验要求、报表进行梳理和统一,同时,保证我们数据录入的标准化、结构化,为后期数据的提取打下坚实的基础。这是一个比较繁杂的基础工作,是质量数字化的有效保障,一定要做实、做细。
3.评估基础设施,必要设备更新换代,以智能化确保数据化的推行
数字化必然需要一定的设备支持,比如,一些繁杂、高频工序的数据采集,单靠人工很难保证效率和准确性。因此,事前必须全盘规划,对方案的可行性进行分析和试验,比如,引入传感、打码、扫码装置,更换老旧设备实现参数自动提取等,若还是都靠人工录入,那这只是记录的电子化,不仅会增加了基层负担,也有悖于数字化初衷,应先打牢自身基础。若盲目开展数字化,规划方向错误,最后可能难以推行,反而成为生产的负担,将面临前功尽弃的风险。
4.资源的整合调用,实现产品全生命周期管理
每一个产品都有它的身份,从原材料的领用,到生产过程记录,完工检验出厂,再到现场使用情况的反馈,都应该整合调用数据库中,记录保存,以便追踪管理,在真正意义上实现全生命周期质量管控,任意阶段发现问题都能快速响应、分析处理,保证客户满意。同时,形成问题库,有助于我们举一反三,避免质量问题重复发生。
因此,数字化的核心就是要确保系统间的串联,打破以往数据孤立的格局,依托生产,整合资源,建立数据汇总分析中心。当然更重要的一步是确定公司生产要素,并对生产要素进行数字化转换。比如,生产完成及时度问题,造成生产滞后的因素很多,常规可分为人(员)、机(器)、(物)料、(方法)法、环(境)等方面,各类产品可确定生产节点与要素,系统根据实际执行,统计各个要素的滞后程度,各个要素滞后也自有原因,生产过程中操作者应进行归类记录,以便系统自动识别。
如此层层深入,便可形成直观的报表及控制曲线,观测生产症结所在,结合精益工具的运用,便可实现针对性地改善,充分发掘出数据蕴含的价值。
5.依托专业团队,加强部门合作,提升职工素养
装备制造企业缺少专业的信息化人才,一般较难靠自身实现数字化,都需要依托专业数字化团队。但企业不能只是简单的外包,应有专人投入到数字化系统的构建中,主导团队展开充分调研,及时传达需求、解决问题。部门之间要相互协作和支持,切勿各自为政,要建立或引入信息化建设管理制度,形成完善的战略管理体系。同时这也是我们数字化人才培养的契机,要保证后期整个系统的运作和维护。企业要不断提升基层员工的数字化意识,表达推行数字化的魄力与决心,如此才能保证大家迎难而上,取得成功。
四、数字化过程中的难点及注意事项
数字化规划中,我们应保证系统的以下性能和要求。
1.保证系统的适用性与先进性
需采用成熟可靠的硬件产品和软件技术构建开发框架,保证系统运行稳定。系统设计要人性化、界面友好、具有可操作性、引导性、帮助性、容错性等。因系统终端用户是人,并且大多是基层工作人员,所以界面应尽量简洁明了,权限分明。系统要具备较好的兼容性,系统功能使用不应受操作系统版本的限制,保证数据可跨平台传输。
2.保证系统的开放性与集成性
系统应采用国际开放式标准技术,具备良好的接口开放性和快速的二次开发的特性。可采用松耦合构件技术方式,快速响应业务需求的变化,有步骤地支持系统的扩展完善和应用,适应公司未来业务变化、发展的需求。系统各层次的信息要能实现充分的交流和共享,各模块之间功能和数据界定清晰,消除信息孤岛。结合实际使用需求,充分考虑用户数限制,并发数限制等条件。
3.保证系统的可靠性与安全性
合理的配置,保证系统的连续、有效稳定运行和快速响应。应考虑完善的数据与系统的容灾备份实施方案及紧急恢复预案,确保数据不丢失。例如,采用双机互备运行方式,提供安全的恢复手段,数据库发生灾难性崩溃导致数据丢失时,也可以根据备份进行恢复数据。当然,使用安全也不容忽视,若为保密数据,必须保证内外网分离,设置严格的角色认定程序,业务隔离,保障终端设备安全、生产控制系统安全和数据安全。
五、结语
企业数据化、信息化很难一蹴而就,需要基础的累积,资源的整合,全盘的规划,再通过精准、扎实地推进,才能逐步地实现,切忌操之过急,否则可能前功尽弃。整个过程会有曲折,但不应气馁,坚定信心,扎实做好调研工作,听取基层操作者的呼声,并努力实现,以此打下良好的推进基础,促使企业逐步走向数字化道路。
以上是关于装备制造业数字化的内涵策划与实施的主要内容,如果未能解决你的问题,请参考以下文章