多机型手机外观清洁与检测设备设计
Posted 深圳信迈科技DSP+ARM+FPGA
tags:
篇首语:本文由小常识网(cha138.com)小编为大家整理,主要介绍了多机型手机外观清洁与检测设备设计相关的知识,希望对你有一定的参考价值。
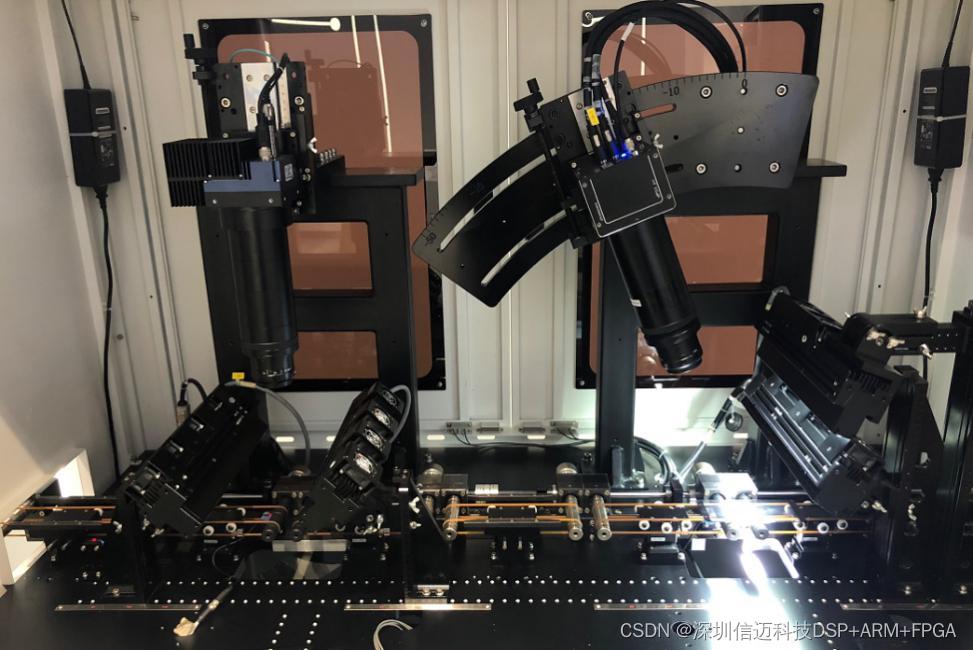
随着德国“工业 4.0”和美国“工业互联网”的发展,我们国家也提出了“中
国制造 2025”应对第四次工业革命
[14]
。“中国制造 2025”的首要目标就是智能
制造,而智能制造就必须结合高度自动化、高度数字化和高度网络化等,未来中
国将在自动化生产和视觉检测行业迎来快速的发展
[15]
。在接下来的一段时间内,
国内越来越多的工厂将大量引进自动化设备。结合目前客户需求及工厂的实际生
产状况,手机相关的设备将在其中占据很大的比重,比如从前端屏幕的切割、清
洗、检测等到后期各个阶段成品的组装、外观的清洁、检测等
[16]
,都可以通过自
动化设备完成。
1.2.1 检测设备国内外研究现状
在国外,工厂智能化程度较高,很多作业都是借助自动化设备完成。近些年
来,随着视觉领域及工业相机的发展,视觉相关的检测设备迎来了高速的发展,
比如使用CCD定位、使用相机进行量测、使用3D相机扫描产品外观轮廓等。虽
然一些视觉相关的检测设备已经成功研发使用,但是产品外观缺陷检测相关的设
备的开发依然有着较大的提升空间,其主要依赖于所使用的缺陷检测技术。相比
国内,国外的视觉检测技术开发较早。上个世纪意大利的Mitra.S.K和Parker.J.M
设计了一款可辨别几十种缺陷的视觉检测单元
[17]
。英国的Latham.V和Nixon.M开
发研制了应用于平板玻璃的视觉检测系统
[18]
。德国的Schmiedl进一步分析研究了
浮法玻璃制作阶段相关的缺陷检测系统
[19]
。但目前大量的屏幕缺陷算法基本都是
通过阈值、边缘检测、方差、灰度直方图等有关的一阶统计方法。比如来自韩国
的Kim及其团队提出了一种可以自动对点状缺陷检测的方法,根据采集到的图像
的局部灰度统计特征,利用不同尺度的自适应阈值对缺陷进行处理
[20]
。又如Tsai
采用傅立叶变换去除缺陷背景干扰,但弊端是时效性效果不佳
[21]
。You-Ching Lee
和Cheng-En Shie等提出一种运用累计差异与多分辨率背景相减的检测方式,弊端
是对装置稳定性要求高
[22]
。研究发现,在频域处理图像进行缺陷检测有着非常不
错的效果,但会带来昂贵的计算开销,而且处理时间很长,不适合在工业生产上
应用
[23-26]
。由上述分析可知,大部分缺陷检测算法都有它的局限性,不能很好的
应对一些缺陷不明显、对比度低的情况,亦或者处理时间长,成本大,不适合工
业推广应用。因此开发手机外观检测设备就有着很大的难度,需处理大量的图像
信息。虽然相比国内国外导入手机外观检测设备时间较早,但目前开发的设备也
主要应用于尺寸固定的产品。造成此种现象的主要原因是设备开发前期主要应用
于新机检测,产品数量大,型号固定,不存在混料生产的现象,对手机的外形尺
寸没有太多要求,但也大大限制了设备的使用范围,不能满足不同尺寸手机的检
测。
近些年来,国内的检测技术也在不断的提升,比如2010年,张舞杰等人
[27]
采用拟合圆和直线的方法研究电池表面缺陷的检测;2013年,杜柳青等人
[28]
检测
磁瓦图像是否具有缺陷时,通过提取物体的混沌特性参数进行识别,并取得了良
好的效果;2014年,王新新等人
[29]
提出了基于机器视觉理论的TFT-LCD缺陷检测
系统,得到了一种很好的耦合检测方法,大幅度提升了缺陷识别率;2018年,张
刘赟
[30]
研究手机金属板表面缺陷检测时,设计了非局部均值去噪算法FoPLBP算
法,并取得了良好的效果。为应对越来越激烈的手机市场,伴随着国内检测技术
提升及国内自动化行业的兴起,很多工厂从一开始引入国外检测相关的设备到逐
步国产化替代。同时国内自动化设备水平也已经有了很大的提高,已经可自主开
发设计检测相关的设备,比如某工厂开发的2.5D屏幕检查设备,如图1.4所示。
由于市场的需求,国内手机外观检测相关的设备也开始研究开发,一些手机
加工工厂也开始大量引进相关的设备,满足生产需求。但现有的设备也同样存在
一个问题,设备只能应用于一款外形尺寸固定的产品
[31]
,对于不同尺寸的机型设
备无法做到兼容,因此检测的范围就受到了很大的局限,这也是一些工厂不愿导
入自动化检测设备的原因之一,因为对于小批量的待检产品而言,成本太大了。
手机颜色对手机清洁过程没有影响,主要跟检测过程中线
阵相机采图时打光环境有关系,不同颜色的手机需要变化光源亮度。如图 2.6 所
示,设备采用多个线性光源,光源强度可变,系统根据不同颜色的手机调整光源
亮度,保证最佳打光效果。
为满足不同客户的需求,当客户端不提供手机机型信息时,在不改动整体设
计思路和外形尺寸的基础上,通过其他两种设计方案仍可达到相同的效果,满足
设备正常使用。
第一种方案如图 2.24,设备设计方式跟原来类似,仅在原基础上加装一个激
光位移传感器用以检测手机厚度尺寸。具体方法是:用一个已知厚度(如 8mm)
手机作为基准手机,激光位移传感器测量距其上表面间距,得到一个数值 A。然
后投入实际需求检测的手机,用同样的方式得到一个数值 B,计算得出手机厚度
尺寸为 8+A-B。手机长度和宽度信息可通过更换成绝对值编码器的伺服电机来获
取。之前使用的增量式编码器断电后需要重新回原点,即电源发生故障时会引发
轴位置的丢失,无法输出电机轴转动的绝对位置信息,而且有零点累计误差。而
绝对式编码器由机械位置确定编码,无需记忆,不需要回原点,也不用计数,可
根据实际需求实时读取位置,且可保持掉电位置,无需担心掉电问题。通过使用
绝对值编码器,实时读取现有状态下位置,当居中夹紧手机时,即可根据当前读
取的数值得出手机长度和宽度的尺寸信息。
第二种方案如图 2.25,在第一种设计方案的基础上新增一个位移传感器,用
来读取手机长度和宽度尺寸信息,具体方法是:用一个已知长度(如 160mm)
手机作为基准手机,夹紧定位柱居中夹紧手机短边,使手机长边相对平台居中,
记录位移传感器显示到测距板间距的数值 C。当投入实际生产的手机时,用同样
的方式得到一个数值 D,由此可推算出手机长度尺寸为 160+2(C-D)。同样的方
式也可得出手机的宽度尺寸。手机厚度的测量方式跟第一种方案一样,即可得出
手机的长度、宽度和厚度三个尺寸。
中框检测调试:中框线扫相机最佳工作距离为 100mm,调整中框三个
线扫相机位置和角度,调整弧形光源位置和角度,使三个中框相机中心汇聚弧形
光源中心,如图 5.18 所示。将手机任一边缘移至弧形光源中心,查看检测结果,
微调线扫相机位置保证采图清晰,完成中框检测的调试.
检测设备调试问题优化
(1)正反面检测机构优化
如图 5.20,设备初期设计时,正反面检测机构采用一个线阵相机加上下两个
线性光源的方式进行检测,其中相机相对竖直方向倾斜 15°,通过角度滑台轻微
调节角度。调试过程中发现两个比较严重的问题,第一是线阵相机采集厚度差异
较大手机图像时,图像非常模糊,无法进行图像识别,这是由于线阵相机景深仅
有 0.3mm,无法兼容厚度差异较大的手机;第二个问题是光源打光效果不理想,
由于手机种类繁多,且颜色各异,配备光源数量较少,角度也不能满足所有机种,
目前的光源结构也无法满足设备需求。如图 5.21 可知,更改后的相机改为竖直
状态,缩小了整体机构,同时在 Z 方向加了一个线性模组,模组重复定位精度
为 1μm,可根据不同厚度的手机上下移动相应的距离从而解决了相机景深问题。
将上方线性光源拿掉放到下方光源对侧,两个侧面也加了一组补光,相机下方增
加了同轴光源,即手机上方、左右、前后均有光源。实际作业中可根据不同颜色
手机自动调整每个光源光线强弱,使每个手机均处于最佳拍照环境,解决了设备
打光问题。
(
2)中框检测机构优化
如图 5.22,中框检测机构主要是有三个线阵相机和一个弧形光源组成,三个
线阵相机呈上中下状态分布,需将三个线阵相机的焦点汇聚到一个点,且该点与
弧形光源中心重合。由于第一代设计时考虑到安装的便利性,将弧形光源安装在
了正反面机构上,因此弧形光源与线阵相机不在一个整体模块下,调试时无法固
定相对位置,需要反复的调试相机和光源不同的位置才能达到合适的效果,调试
进度非常缓慢。整个过程也没有明确的参考,也增大了调试的难度。为提高调试
效率,如图 5.23,对机构进行了修改,将光源和三个线阵相机整合到一个机架上,
使其相对位置不变。机架安装在一个小底板上,可满足整体左右、前后调节,同
时机架整体相对小底板角度可调。优化了上中下三个线阵相机的调节方式,使其
均可轻松调节。如图 5.24,后续又对设备所有相机和光源可调节方向均加了刻度
指示,使各个调试环节均具有参考位置标准,加快了整体的调试速度,如中框检
测机构初次调试时话费了将近一周的时间,优化后的机构仅需三个小时即可完成
相关调试,正反面机构之前需要 1.5 天时间调试,更改机构、新增标尺后仅需 2H
即可完成调试。整体的调试效率得到了大幅度的提升,大大节省了整个项目的调
试时间和人力,更快速的响应客户的需求。

以上是关于多机型手机外观清洁与检测设备设计的主要内容,如果未能解决你的问题,请参考以下文章
谈谈 老罗和"锤子"
手机各机型尺寸比较
硬件软件全面升级 HTC Butterfly S评测
MOTO Z模块化设计,你的手机你自己决定!
使用曲线将输入范围弧形拇指连接到滑块
手持终端外观设计像似手机形状